Thermal-Mechanical Modeling of Module-Level Failure Mechanisms
DuraMAT uses finite element modeling to better understand how photovoltaic (PV) module deployment environments induce the damaging thermal and mechanical stresses leading to module degradation, via delamination, cell fracture, and interconnect fatigue among other mechanisms.
These computational simulations capture key degradation physics at the length- and time- scales of interest and are tightly coupled with experimental material and module characterization efforts to receive information for model inputs and validation while enriching interpretation of measurement results.
Full-scale module models have been developed that accept direct environmental loads including wind pressure, temperature changes, rack mounting constraints, and gravity. Cell-scale sub-models have also been developed, which couple to full module results to resolve detailed mechanisms including interconnect thermal-mechanical fatigue and interface delamination stresses. All models may be utilized parametrically for optimization, uncertainty quantification, and sensitivity studies to understand how specific material and design choices affect the module package.
The goals of this modeling capability are to enable more accurate lifetime predictions, more representative accelerated test specification, and allow for optimized module material selection and design for durability.
Core Objective
Multi-Scale, Multi-Physics Modeling
Location
Sandia National Laboratories
Applications
Models may be used to rank stressors by potential for damage (i.e. thermal cycling vs. mechanical loads), as well as identify the effects of coupled mechanisms. Design optimization and sensitivity analyses for both materials and geometries are another key application area.
Availability
Insights from this capability are made public in academic journals. Modeling capabilities are available to DuraMAT consortia members with a collaborative project.
References
James Hartley and Scott Roberts, "Effects of Solar Cell Materials and Geometries on
Thermally Induced Interfacial Stresses". Proceedings of the 45th IEEE PVSC Conference, Waikoloa,
Hawaii. June 10-15, 2018. pp. 3179-3184. DOI: 10.1109/PVSC.2018.8547399
James Y. Hartley, Ashley Maes, Michael Owen-Bellini, Thomas Truman, Edmund Elce, Allan
Ward, Tariq Khraishi, Scott Roberts, "Effects of Photovoltaic Module Materials and
Design on Module Deformation Under Load". Proceedings of the 46th IEEE PVSC Conference, Chicago,
IL.
June 16-21, 2019. pp. 0511-0516. DOI: 10.1109/PVSC40753.2019.8980842
Ashley Maes, James Hartley, Christine Roberts, “Thermal and Viscoelastic Behavior
of Polymer Films Used as Photovoltaic Module Encapsulants”. 90th Annual Meeting of
The Society of Rheology, Houston, TX. October 14-18, 2018.
DuraMAT Webinar Series, October 2019: “Multi-Scale, Multi-Physics Modeling Capabilities towards Predicting PV Reliability,” presented by James Hartley, Sandia.
Contact
To learn more about this project, contact James Hartley.
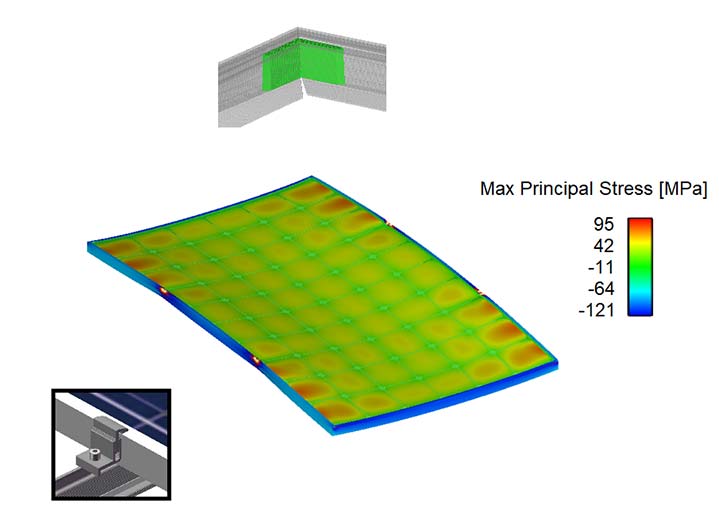
Modeled module state under environmental loading conditions with resolution of mounting and framing effects. Full-scale module models may be used to answer questions relevant to individual cells and reduced-scale accelerated testing, among others.